The Isuzu Difference: Engineered for Efficiency
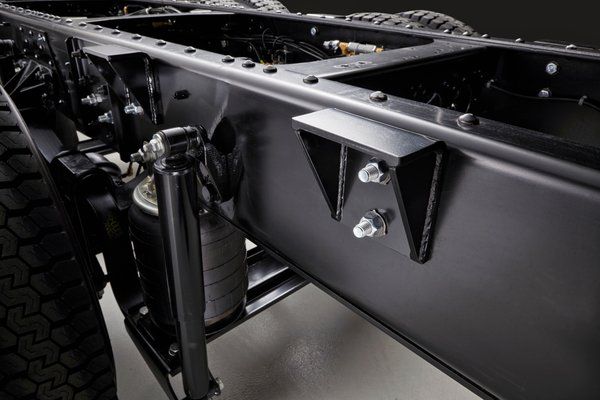
Having only recently released the safest and most well-supported Isuzu N Series ever to hit the Australian market, Isuzu Trucks continues to bolster its offering both on and off the road.
The Australian truck market leader has been underpinned by exceptional product for decades, but it could be argued that Isuzu’s unwavering popularity has been cemented by the local engineering nous behind that product.
Based out of the brand’s headquarters in Melbourne’s western suburbs, Isuzu Australia Limited’s (IAL) Product Development Centre (PDC) and local Engineering team are responsible for a range of critical projects, from full-scale developments and testing to localised suitability refinements and everything in between.
Local knowledge
Isuzu’s Engineering Support Manager, Jeff Gibson, said IAL’s highly regarded PDC is at the coalface when a new model, a localised variant or some new technology lands in the country.
“What many people may not realise is just how much work goes into a local release of an Isuzu product. That could be anything from a new towing assembly to the development of a bullbar, right through to the release of an entirely new range, such as the latest N Series range we’ve just launched,” Mr Gibson said.
“The scope of the work is immense. The next time you sit in a new truck, know that thousands of hours have gone into it here in Australia, regardless of where in the world the production line might be.”
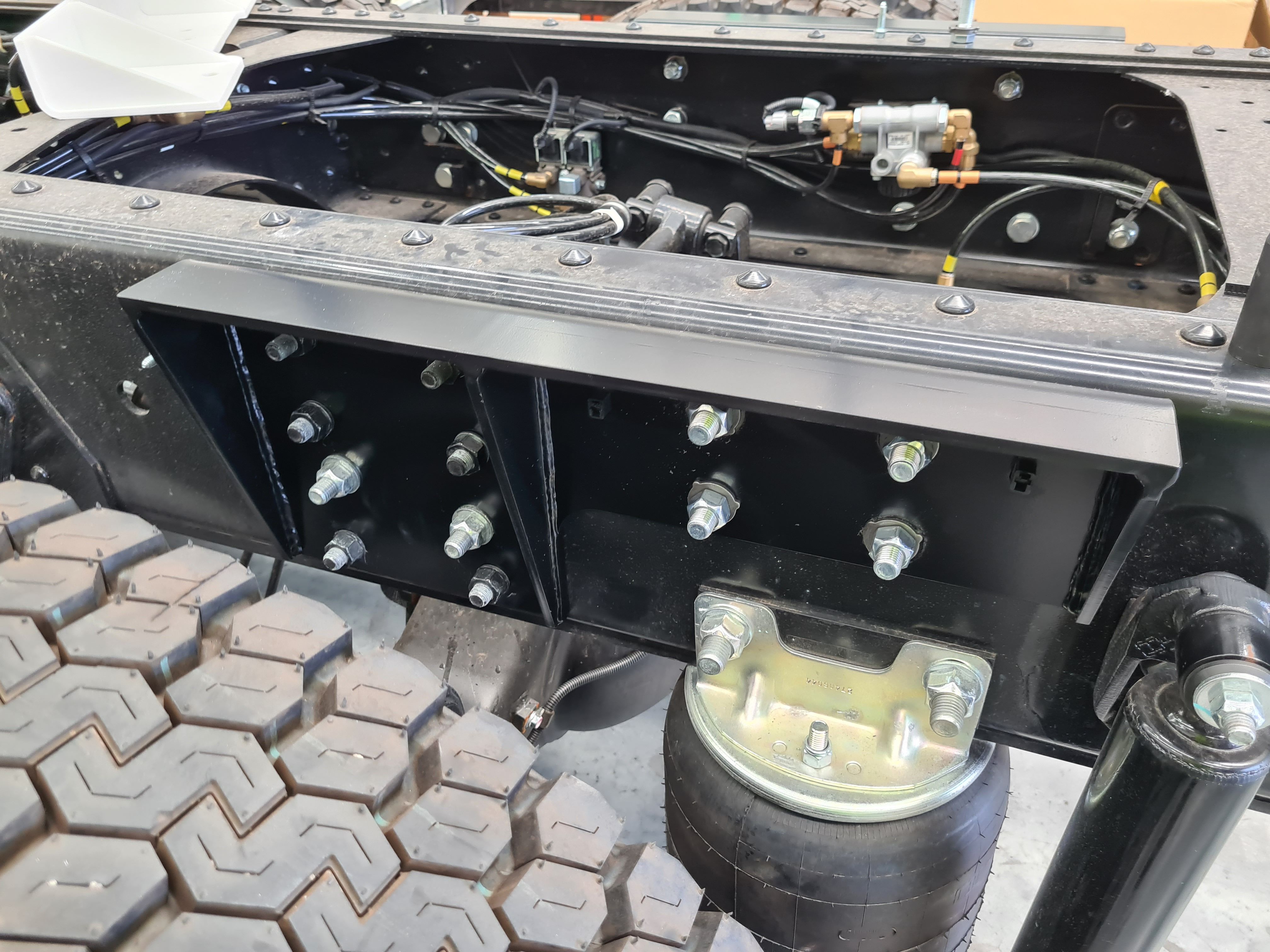
CAD
Whilst at the cutting-edge of technology coming from abroad, Isuzu’s local Engineering team doesn’t always land the plumb jobs. Processes need tweaking, supply chains need feeding and much of the innovation had to happen yesterday.
Mr Gibson clarified further, “An example of this is our recent work around computer aided design or ‘CAD.’
“This was an efficiency born out of the pandemic and one that’s been a genuine win-win for all involved,” he said.
In an industry first for a Japanese OEM, Isuzu staff both locally and in Japan have worked to create a portal to provide 3-Dimensional (3D) CAD models for Model Year 21 and beyond access for approved truck body builders.
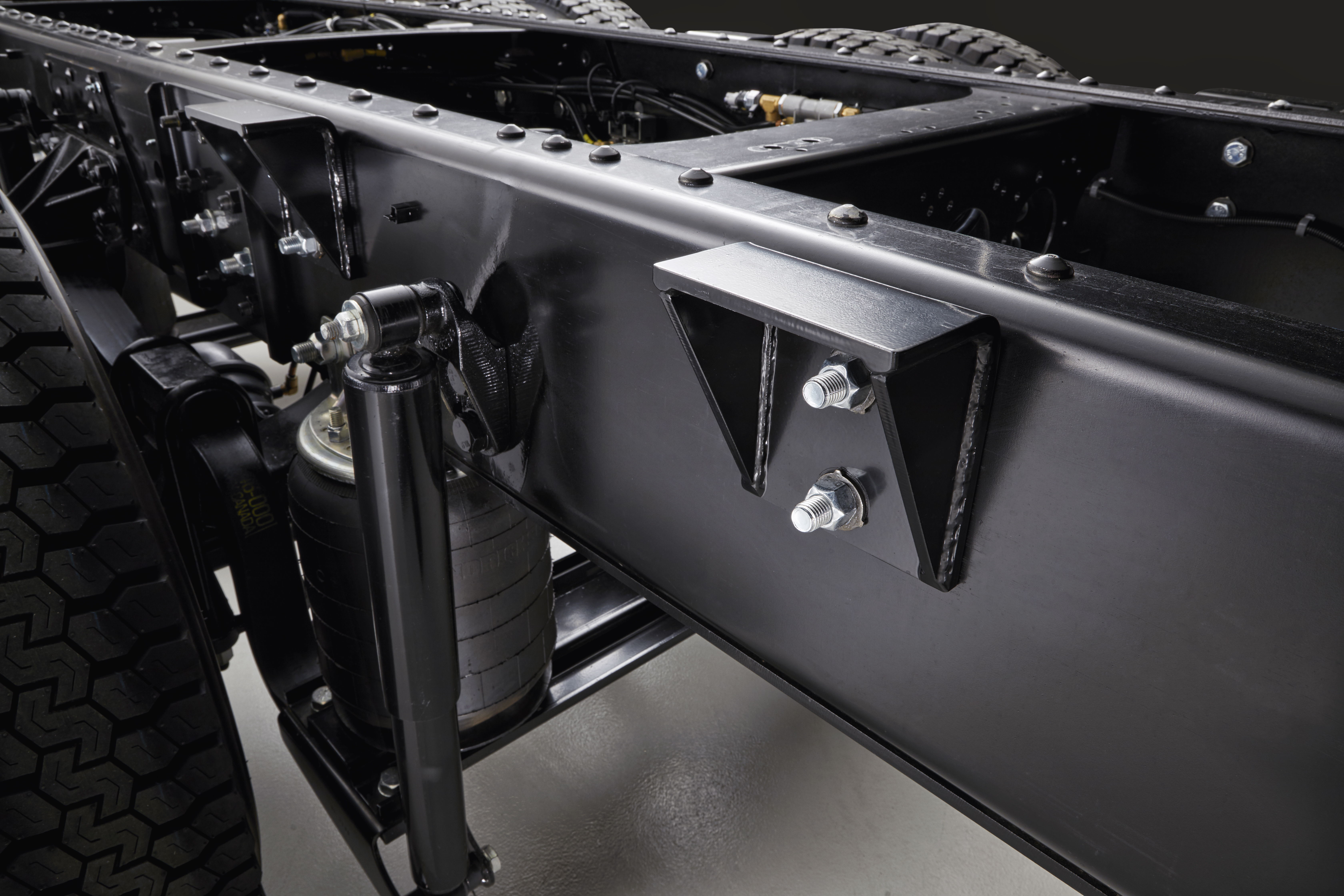
Due to increased industry demand and supply chain limitations, many Australian truck body builders are pushing forward scheduled body design work, well before a customer’s truck has arrived or even been shipped.
Having millimeter perfect 3D CAD modelling in hand before the truck has arrived means a body and the all-important mounting system can be designed and manufactured well in advance.
“This speaks further to the complete Isuzu package, our focus on better supply chain operation and ultimately, to our customers receiving their truck as soon as possible,” Mr Gibson said.
QR capturing
In another industry first for IAL’s Engineering Department, the brand has recently implemented the use of QR code labels - attached to new model trucks - as part of responding to requirements under the Road Vehicle Standards Act 2018.
“We made a decision to once again take the opportunity to look for efficiencies for our customers and find a better way of utilising existing, familiar technology,” Mr Gibson explained.
“We developed a website framework at IAL whereby the individual information of each truck model can be stored and accessed via individual QR codes attached to labelling on the inside trucks’ door frame.”
Everything from registration and VIN information, identification codes, warranty timelines, gross vehicle mass, combined mass through to the number of seats, can be accessed via a simple QR code scan.
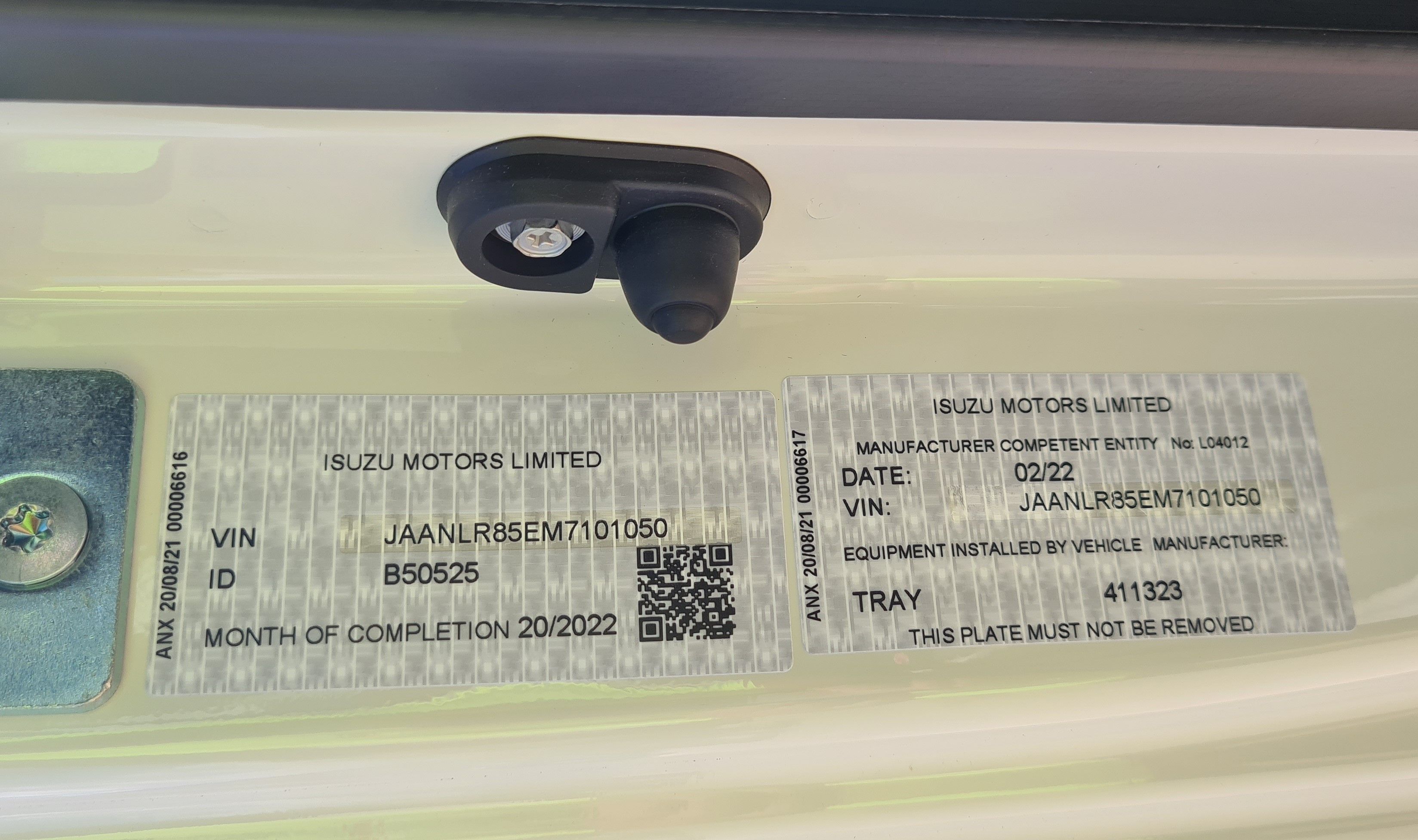
“It’s introductory information but it is now easily accessible for a number of parties, from body builders, insurers, emergency services to the owners themselves.
“The potential for the smarter use of this technology is huge and we’re currently developing further ideas around the user experience of owning an Isuzu truck.”
3D printing
A final example of innovation radiating from Isuzu’s PDC is the advent of additive manufacturing for rapid prototyping using 3D printing.
Put simply, this is the use of 3D printing for quicker design progression and proof of concept for sample prototypes.
This could be something as simple as a mount for camera or an outrigger body mount bracket being tested or could involve more dimensionally accurate pieces.
Isuzu’s Engineering Department has expanded its printing program more recently in the wake of movement restrictions and prohibitive turnaround times, meaning the ability to problem-solve quickly has added to the team’s research and testing capabilities.
The ‘Isuzu difference’
From product testing and refinement to discovering efficiencies in supply chain processes, it’s an approach of constant improvement that helps keep the Isuzu brand on top.
Mr Gibson explained further, “As any student of the Australian truck market will tell you, there’s a level of product parity, in a general sense, between a number of competing brands.
“You can expect to see some fairly similar traits between comparable models, products and services – for the most part.
“What sets Isuzu apart though, is our approach to the bigger picture. It’s a very deliberate attempt to find the best solution for our customers, wherever that solution can be sought.
“It’s the sum of the whole. It’s that Isuzu difference that genuinely makes a difference,” he concluded.
The Isuzu Difference_Engineered for Efficiency.docx
DOCX 26 KB
Sam Gangemi
Arkajon Communications